High Speed Fingerless Paper Corrugation Machine
Products
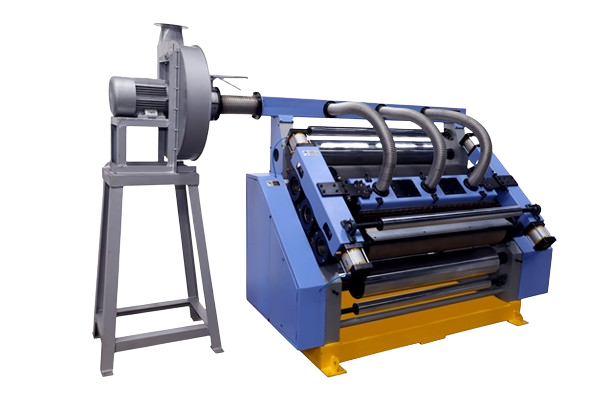
High Speed Fingerless Paper Corrugation Machine
A High-Speed Fingerless Paper Corrugation Machine is an industrial equipment used in the process of corrugating paperboard to create corrugated cardboard, which is widely used in packaging materials. Here’s an overview of its key features and functions:
Fingerless Design:
- The term “fingerless” refers to the absence of traditional suction fingers in the corrugating rolls. This design reduces the chances of crushing and tearing of paper and allows for faster corrugation.
High-Speed Operation:
- These machines are designed for high-speed production to meet the demands of large-scale manufacturing facilities. The speed can vary depending on the model and specifications.
Corrugating Rolls:
- The machine consists of corrugating rolls that impart a corrugated pattern onto the paper. These rolls come in different flute profiles, such as A, B, C, E, etc., each serving specific packaging requirements.
Single Facer Unit:
- The single facer unit is a crucial component that corrugates the paper. It typically consists of a set of heated corrugating rolls and pressure rolls.
Gluing Unit:
- After corrugation, the machine may have a gluing unit to apply adhesive to one side of the corrugated medium. This is followed by the application of the liner on top.
Sheet Cutter:
- Some machines may include a sheet cutting unit to cut the corrugated board into sheets of desired lengths.
Control Systems:
- Modern machines often come equipped with advanced control systems that allow for precise adjustments of speed, temperature, and other parameters. This enhances efficiency and ensures consistent product quality.
Material Handling Systems:
- These machines are often integrated into larger production lines with material handling systems for smooth and continuous operation.
Automatic Stacker:
- A stacking unit may be included in the machine to accumulate and stack the finished corrugated sheets neatly for easy handling.
Maintenance and Safety Features:
- Regular maintenance is essential to keep the machine running smoothly. Safety features such as emergency stops and protective guards are incorporated to ensure the well-being of operators.
It’s important to note that the specifications and features of a High-Speed Fingerless Paper Corrugation Machine can vary among manufacturers. The choice of a specific machine depends on the production requirements, the type of corrugated board needed, and other factors specific to the manufacturing process.
Plate-Based Printing: Flexo printing uses flexible relief plates made from materials like rubber or photopolymer. These plates are mounted on cylinders and transfer ink to the printing substrate.
Versatility: Flexo printers are used for printing on various substrates, including paper, cardboard, plastic, film, foil, and even fabric. This versatility makes them a popular choice for packaging materials and labels.
Fast Printing Speeds: Flexo printing is known for its high-speed capabilities, which make it suitable for large production runs.
Multiple Color Printing: Flexo printers can use multiple ink stations, allowing for multi-color printing in a single pass.
In-Line Processing: Many flexo printers are equipped with in-line finishing and converting options, such as die-cutting, laminating, and slitting, which can significantly reduce post-printing processing time.
Precision Registration: Flexo printers offer accurate registration of colors and images, ensuring that the final printed product looks sharp and well-aligned.
Water-Based and UV Inks: Flexo printers can use a variety of inks, including water-based and UV inks, depending on the specific requirements of the job.
Low Waste: They generate relatively low levels of waste due to their ability to print directly on the substrate.
Customization: Flexo printers can be customized to meet the needs of different industries and applications, from food packaging to labels and newspapers.
Cost-Efficiency: Flexographic printing can be cost-effective for long runs, as it can achieve high speeds and efficient ink utilization.
- 32″
- 36″
- 42″
- 46″
- 52″
- 56″
- 62″
- 70ft.
- 70ft.
- 70ft.
- 15 kw.
- 15 kw.
- 18 kw.
- 21 kw.
- 24 kw.
- 27 kw.
- 30 kw.
- 3 H.P.
- 5 H.P.
- 5 H.P.